Combination Product Industry News & Guidance
Sharing device-related information and wisdom
that will help you succeed
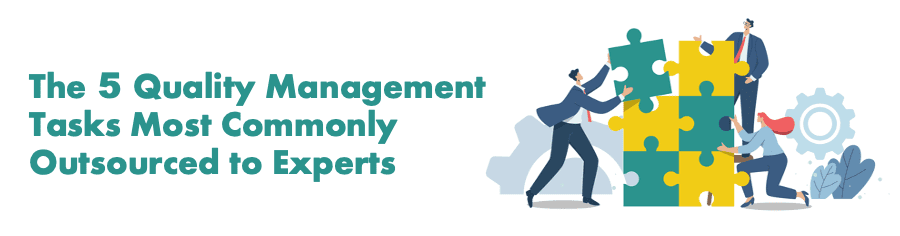
Last week the alert came on in my SUV that in 500 miles I needed an oil change. I thought to myself “I am a smart and handy woman who could probably do a little research and figure out how to do this on my own. Save a little money.” Then I started watching a video and realized, with each new step they presented, that I had at least one or two more questions and unknowns to figure out. After a handful of videos, searching for the one that would fill in all of my knowledge gaps, I wondered, “If I added up all of the time it would take me to figure this out and then actually do it, including the potential mistakes and redo’s that may include, is it really worth doing myself?”
When I estimated that time, multiplied by what I normally make in an hour of work, I quickly realized this DIY fantasy sounded much better than the reality. It made more financial sense to hire a professional to do it quickly, efficiently and right the first time. And between my work, my kids, and everything that life was throwing at me, did I really have the time to take this new project on myself?
A few days later, I was in a meeting with our Director of Technical Services, Carolyn Dorgan, talking about our quality management services. As we caught up before digging into work, I told her of my oil change debate. It got us talking about the kind of quality management system tasks that our clients generally overlook with regard to how much easier, more efficient, and cost-effective it is to outsource to experts vs. taking it on internally. The tasks she identified were:
- Mapping out design verification sample size
- Creating manufacturing sampling plans
- Remediating quality audits
- Administering quality plan audits
- Perform prior-to-approval inspection preparedness
The sampling services made the list because they are, as Carolyn noted, “activities that our experts can do in their sleep.” Through their efficiencies, we have found that our consultants can save clients time and money pulling these items together on their behalf. They also provide more accurate plans for success due to their vast experience in this area. For the audit and inspection tasks, thanks to our unique strength in combination product regulatory affairs, in addition to being cost- and time-saving, SCI consultants reduce risk and put the product in a much stronger position for approval the first time through a second pair of practiced eyes applying industry best practices and FDA insider knowledge.
Like me and my oil change, our Pharma clients often have very capable talent on staff who could figure out how to handle these quality management projects, but sometimes these people don’t have the right practical experience to do it efficiently, sometimes they need outsider insights or second opinions, and sometimes they simply need to prioritize their time elsewhere. That’s where Suttons Creek steps in. Reach out if you want to explore how we can help you get your QMS tasks done right.