Combination Product Industry News & Guidance
Sharing device-related information and wisdom
that will help you succeed
Creating A Design History File (DHF) That Gets Approval
Combination products have unique design and regulatory requirements from those of drugs and biologics alone. One of which is the necessity to submit a Design History File for regulatory approval. The US Food and Drug Administration (FDA) has established regulations and guidelines that require combination product manufacturers to create and maintain a DHF. Specifically, 21 CFR 820.30 requires them to establish and maintain a DHF for each type of device they manufacture. Additionally, the International Organization for Standardization (ISO) has developed standards, such as ISO 13485, that provide guidance on the contents of a DHF. To ensure compliance, it is your job as a combination product marketing authorization holder to create a complete design history file (DHF) for your combination product in addition to any DHF created by a supplier or partner.
Our team of experts at Suttons Creek has a multitude of experience in servicing the DHF needs of Pharma’s biggest players. We review existing DHFs for regulatory gaps, help set DHF strategies, install effective systems, and even support the actual work needed to get your design history file completed. This hands-on know-how has formulated a deep understanding of Design History File requirements and working best practices that we will share with you in this article. To start, let’s make sure you know exactly what a DHF is and what goes into it…before we get into how to do it the right way.
Design History File Definition
A DHF is a compilation of records and documentation that describe the design and development of a medical device or combination product (see image below). The purpose of a DHF is to provide a comprehensive overview of the product development process and to demonstrate that the product has been developed in accordance with your outlined Design Development Plan and Design Control Process. The DHF is a critical component of a medical device or combination product’s regulatory submission and must be maintained throughout the product’s lifecycle. It can take electronic or paper form and can be a folder containing documents or an index of references.
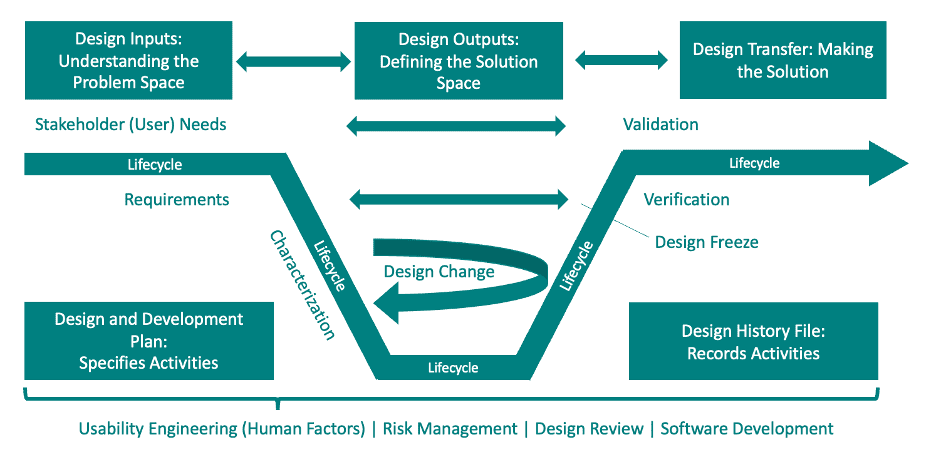
Typical Documents Included in a DHF
The DHF for a combination product should contain documentation that demonstrates compliance with regulatory requirements, including product design, development, verification, validation, and manufacturing. The following documents, and subsequent supporting documents, are typically included in a DHF:
- Design and Development Plan: Outlines the product’s design and development process, including milestones and timelines.
- Design Inputs: Documents the product requirements, user needs, and design constraints.
- Design Outputs: Documents the results of the design process, including design specifications, drawings, and prototypes.
- Design Reviews: Documents the reviews of the product design throughout the development process.
- Design Verification and Validation: Documents the testing and evaluation of the product to ensure it meets design requirements and user needs.
- Change Control: Documents any changes made to the product design and the rationale for those changes.
- Design Transfer: Outlines the process of transferring device design from the product development team to the manufacturing team for production. Design transfer involves ensuring that the design (device and drug component) is properly documented and communicated and that the manufacturing process can produce a product that meets design requirements and regulatory requirements for safety, efficacy, and quality.
- Risk Management File: Documents the identification, evaluation, and management of product risks.
- Usability Engineering File: A record of the process used to ensure that the device component of the combination product is safe and effective for its intended use.
- Clinical Data: Documents the results of any clinical studies conducted to support product safety and effectiveness.
- Manufacturing and Quality Control: Documents the manufacturing process and quality control procedures used to ensure the product meets regulatory requirements.
- Device Master Record / Master Batch Record: Detailed instructions for the production of a combination product that serves as the basis for the production of the product. The DMR or MBR includes all of the information needed to manufacture the combination product, including the device design specifications, manufacturing procedures, and quality control procedures. It also includes the specifications for the drug component, if applicable, and any other components that are part of the product.
Platform Documents
All of this DHF content needs to be created for each combination product submitted for FDA approval. This workload can be streamlined through the creation of Platform DHFs and Platform DHF Documents that can be used across multiple devices.
A platform device is a medical device that serves as the basis for the development of multiple products or product variants. A platform document is a comprehensive document that contains all the necessary information for developing products based on that platform device. The platform document serves as the basis for the platform design history file (PDHF), which contains all the documentation related to the development of products based on the platform device.
A single Platform DHF (PDHF) can be used for multiple devices when applied to:
- different colors or SKUs of the same device
- clinical and commercial combination product versions
- special device versions for special markets (ie. same device, alternate labeling)
- different drug products
- referencing for individual components of a similar device (becoming part of a “Kit DHF” that incorporates reference to multiple DHFs)
Platform DHF Documents can be shared across combination products and plucked for inclusion within those products’ own unique DHF. For example, source material platform documents may be the same for products 1, 2, and 3, while design output platform documents may apply to products 2 and 3, and process/procedure platform documents may apply to products 1 and 3.
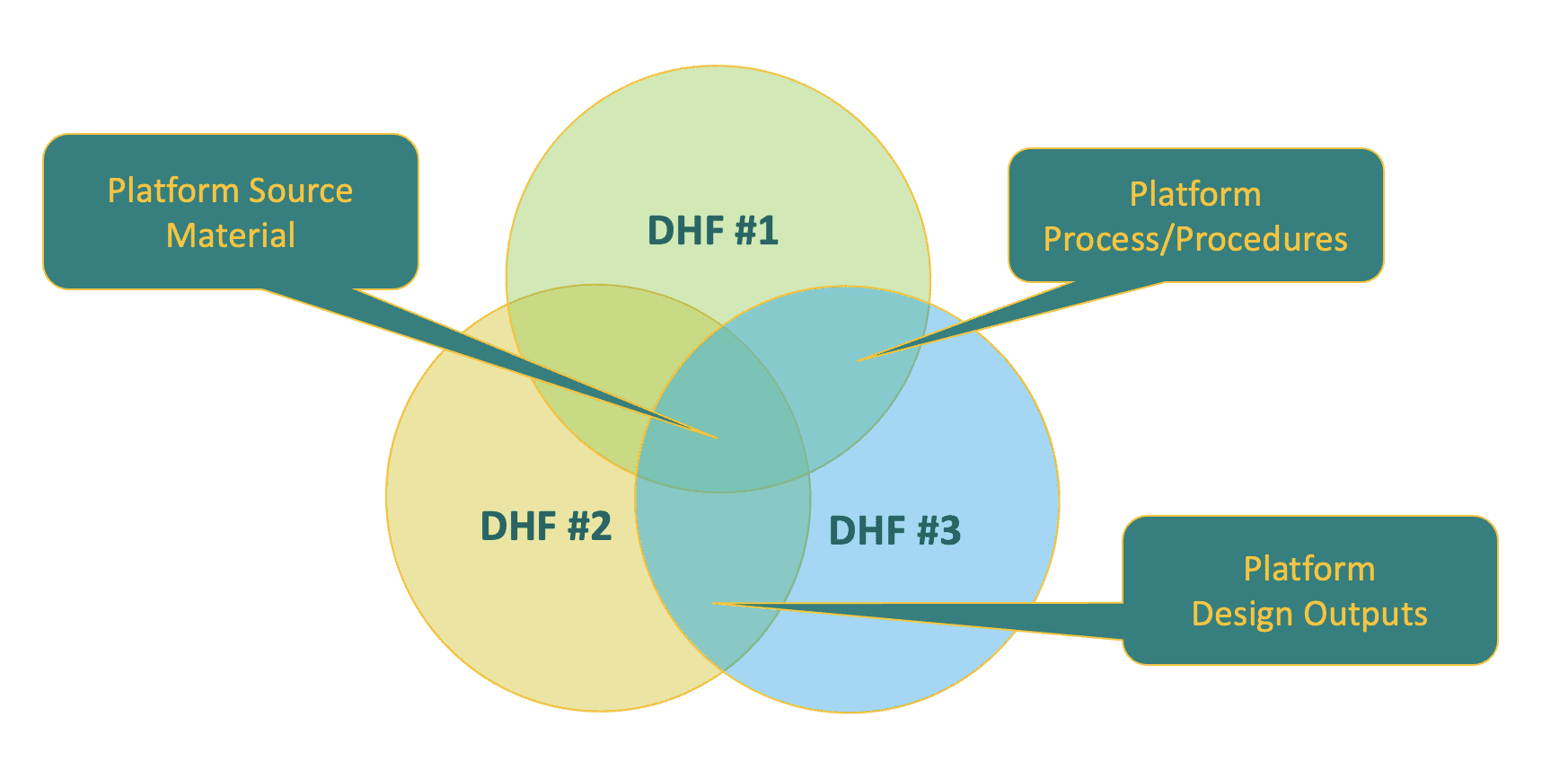
Bridging Strategies for DHF Creation
Beyond utilizing platform documents, another method for streamlining DHF creation for a new product is to execute a bridging strategy, which can address gaps in your regulatory framework without repeating work done for another product. This strategy facilitates the creation of a comprehensive design history file (DHF) by linking data from a previously approved product with a modified/updated product, a similar product, or a new combination (new device with the same drug / new drug with the same device). A bridging strategy can be used to demonstrate that a modified or updated product is safe and effective, based on the safety and efficacy data from the previously approved product and to address any gaps in the regulatory framework that may occur when developing a combination product that is similar to one for which a DHF already exists. Bridging strategies, when used, must be documented in your design history file (DHF).
There are several key steps that should be taken when executing a bridging strategy for a combination product:
- Identify any regulatory gaps: The first step in executing a bridging strategy is to identify any regulatory gaps that may exist. This can be done by reviewing the regulatory requirements for the combination product and identifying any areas where data or information may be lacking.
- Identify the bridging strategy: Once the regulatory requirements are identified, the next step is to identify the bridging strategy. This may include linking the data from the previously approved product, conducting additional studies, or using other data sources.
- Identify existing data or information: The next step is to identify any existing data or information that may be used to bridge the regulatory gap. This may include data or information from previous studies or from similar products.
- Determine the relevance of existing data or information: Once existing data or information has been identified, it is important to determine the relevance, reliability, and accuracy of the data or information to the combination product. This will help to ensure that the data or information can be used to bridge the regulatory gap.
- Analyze impact on product safety and effectiveness: The bridging strategy should not have a negative impact on product safety or effectiveness. Any potential risks should be identified and addressed.
- Perform gap analysis: A gap analysis should be performed to determine whether the existing data or information is sufficient to meet regulatory requirements. If there are any gaps, additional data or information may need to be collected.
- Develop a bridging plan: Based on the gap analysis, a bridging plan is developed to address any gaps in the data. The plan may include additional bench or clinical studies or the use of other data sources to fill the gaps and apply improvements.
- Document the bridging strategy: The final step is to document the bridging strategy. This should include a description of the regulatory gap, the existing data or information that will be used to bridge the gap, the relevance of the data or information, the results of the gap and risk analysis, and any additional data or information that will be collected.
Common DHF Creation Problems You Can Avoid
Now that you are familiar with what goes into a Design History File, and both Platform and Bridging strategies that can be used to streamline its creation, you can better understand the complexity of this activity. With so many moving parts and documents to bring together, it is common to run into problems. Here are a few that we have seen when clients called for support:
- Lack of clarity on regulatory requirements: One of the most common problems with the creation of a DHF for combination products is a lack of clarity on the regulatory requirements. Combination products are regulated by multiple agencies, including the FDA, EMA, and other regulatory bodies depending on your global markets, which can lead to confusion on the specific requirements for the DHF.
- Lack of a comprehensive DHF Index: An index should be created by knowledgeable experts at the outset of the project to ensure the necessary information is captured and documented in the final DHF. In addition to an index, creating a reviewers guide can be useful not only for regulatory but for bringing on new team members to a project.
- Incomplete documentation: Another common problem is incomplete documentation. A DHF must include all of the documentation related to the design, development, and testing of the combination product. If any documentation is missing or incomplete, it can result in delays in the regulatory approval process. Using a sophisticated electronic documentation system and creating a mechanism to associate project documents to their related DHF(s) make it much easier to find needed DHF records.
- Lack of functional integration: A DHF for combination products must integrate the design, development, and testing of both the device and drug components. This can be challenging as the two components may be developed by different teams and subject to different regulatory requirements. Communication between the different teams involved in the development of the combination product is critical to the success of the DHF. Poor communication can result in incomplete or conflicting documentation, which can lead to delays in the regulatory approval process.
- Inadequate risk management: Combination products are subject to unique risks, including risks associated with both the drug and device components and user error. If risk management is not adequately addressed in the DHF, it can result in delays in the regulatory approval process. To learn the best practices in risk management assessment techniques, click here to read more.
- Inadequate testing: Testing is an essential component of the DHF for combination products. If testing is inadequate or not properly documented, it can result in delays in the regulatory approval process.
- Incomplete consideration for bridging strategies: Changes in the current product from the product for which you are using bridging documentation can create erroneous information in your DHF. Some overlooked changes are: local delivery adverse reaction profile, manufacturing process, device constituent, intended use, user interfaces, patient population, bioavailability of the drug and/or its metabolic profile in combination with the new product, drug delivery methods, and drug formulation.
Creating a DHF for combination products requires careful attention to detail and an understanding of the regulatory requirements. By proactively addressing these needs, taking preventative steps to avoid common challenges, and working closely with regulatory agencies and suppliers, manufacturers can create a DHF that meets regulatory requirements and facilitates the regulatory approval process.
AUTHORS
Carolyn Dorgan, Director, Technical Services, Suttons Creek, Inc. –Carolyn Dorgan has 10+ years of experience in the Medical Device and Combination Product industries, including 6 years at the FDA leading the Infusion Devices team. Carolyn is active in the international regulatory community through speaking engagements and has participated in over a dozen international standards ranging from infusion devices, to needle-based injection systems, on-body delivery systems, and infant incubators. In addition, her unique approach to product development and risk management has been instrumental in working with products for which there are no established performance or regulatory standards which include pediatric medical devices, novel on-body drug delivery systems, and rare disease combination products. Carolyn has a demonstrated ability for working through complex problems at a system level to implement practical solutions using her multi-disciplinary background which includes engineering, software, cybersecurity, human factors, and business.
Steve Badelt, PhD – Steve is a seasoned expert with over 20 years of experience in combination products, engineering management, systems engineering, and business development. He founded consulting firm Suttons Creek, Inc. in 2012, which has served as the device team for pharma on over 50 combination product programs. Steve values helping others learn and grow, and when he is not consulting on behalf of Suttons Creek, he is advising startups, sitting on industry boards, speaking nationally on combination product and connectivity issues and serving as a Graduate Professor at Loyola Marymount University. LinkedIn: Steven Badelt, PhD